Welding Equipment: Essential Tools for Fabrication and Assembly
Author : Nishant Sherkhane | Published On : 19 Apr 2024
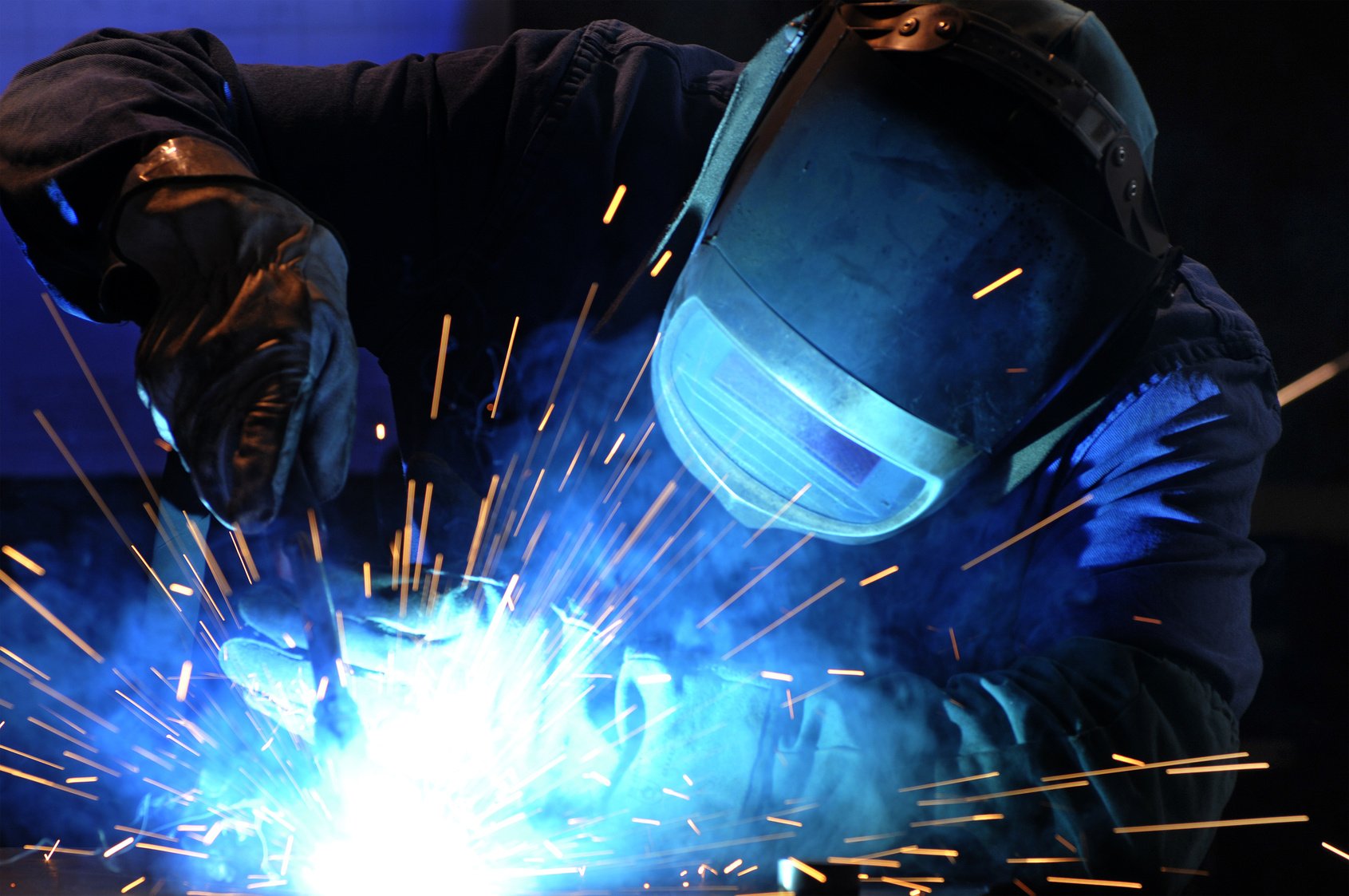
Types
Welding machines: Welding machines are classified based on the welding process they are designed to perform. Some common welding machines include stick welders, TIG welders, MIG welders, and plasma cutters. Stick welders are used for stick (SMAW) welding and operate by creating an electric arc between a consumable electrode and the workpiece. TIG welders are used for gas tungsten arc welding (GTAW) and feature non-consumable tungsten electrodes. MIG welders are suited for gas metal arc welding (GMAW) using consumable solid welding wire as an electrode. Plasma cutters use a very hot, constricted jet of ionized gas to cut through electrically conductive materials like metal.
Wearable Welding equipment: In addition to welding machines, various pieces of protective Welding Equipment are necessary to ensure welder safety. This includes a welding helmet to protect the eyes and face from UV/IR radiation and sparks, protective leather gloves, flame-resistant coat/jackets, safety glasses, and steel-toed boots. Welding helmets are specially designed with an auto-darkening lens that senses the arc and automatically switches to the dark state for better visibility and eye protection during welding.
Accessories: Welding machines also require auxiliary equipment and accessories to perform specific welding processes and techniques. Examples are welding torches, electrodes, filler wires, gas cylinders, regulators, hoses, clamps, and grinders. Welding torches are attachments used with MIG, TIG, and plasma cutters. Electrodes and filler wires are consumable materials specific to stick welding and GMAW/GTAW. Regulators, hoses, and cylinders are needed to supply shielding gases like argon and helium.
Welding Fume Control
Ventilation equipment: Inhalation of welding fumes can have serious long-term health effects, so proper ventilation is a necessity. Portable ventilation units, booth ventilators, and fume extraction arms are commonly used to clear toxins from the breathing zone or draw them away through ducting. This helps improve indoor air quality for welders and others working nearby.
Respirators: When ventilation is insufficient or not practical, respirators are the last line of defense against welding fumes and gases. Half-mask and full-face respirators equipped with appropriate cartridges/filters provide protection from fumes and particulate matter generated during welding, brazing, cutting, etc. Respirator selection is based on the specific processes, materials involved, and expected contaminant concentrations.
Filters: Several filter choices are available depending on the composition of fumes/particulates. For general welding of mild steel and stainless steel, combination organic vapor/acid gas/particulate pre-filters and main filters work well. Specialty high-efficiency particulate air (HEPA) filters are recommended when working with hazardous metals such as zinc, cadmium, chromium, and lead. Regular replacement of filters ensures peak performance.
Welding Positioners and Rotators
Positioning welding equipment: For jobs requiring welding in hard-to-reach positions like overhead, vertical-up, vertical-down, etc., welding positioning systems allow manipulating the workpiece into optimal angles. Boom-style positioners suspend loads and use hydraulic cylinders or motorized screws for smooth manipulation. C-style positioners have two inward-facing arms that hold workpieces vertically or horizontally.
Rotators: Rotating welding tables are used to simplify multi-directional welding on cylindrical or rounded parts by spin-welding them continuously. Motorized welding rotators rotate workpieces slowly and continuously while welding for full-circle welding application without repositioning. They are useful for pipes, pressure vessels, storage tanks, and other tubular structures.
Clamps and Fixtures
Clamping equipment: Clamps, vises, and jigs are used to securely hold workpieces for welding. Common examples include bench vises, C-clamps, welding clamps of various sizes, magnetic bases, pipe rolling fixtures, and purpose-built jigs/fixtures. They prevent slippage and misalignment which can compromise weld quality and safety. Some clamps even allow angular positioning and rotation.
Welding automation: For mass production welding applications, automated welding fixtures allow loading parts in consistent positions for repetitive welding. Robot arms equipped with welding torches perform programmed welding sequences on fixtures or conveyor lines with precision and consistency. This maximizes productivity and product uniformity in high-volume manufacturing facilities.
There is a wide assortment of welding equipment needed to perform different welding processes, ensure welder safety, control fumes/dust, manipulate workpieces, hold joints accurately, and automate welding operations. Proper selection and maintenance of machinery, wearables, consumables, ventilation, and positioning/clamping gear is crucial for quality results and a safe working environment.
Get more insights on Welding Equipment